
01.15.2025 – 3 out, 3 in..



..of and to the kiln on this beautiful Eastern Shore morning.
Yesterday, while 3 pieces cooked to cone 05, I experimented with some glaze application techniques for the shell interiors. The challenge with trying to create some amount of accuracy is working with the unpredictability of glazes, underglazes and stains. Once fired, those things almost never look the same as they did during the application process. So, to the boneyard we go.
On average, I loose 30% of the green or unfired pieces to cracking. The natural oyster is so varied in it’s texture and thickness and clay doesn’t dry evenly when the thickness is too varied, especially at this scale. The most vulnerable areas are the lips where the difference of 1/16″ could mean a solid candidate for an ultimately finished piece or another addition the the “boneyard” under my wife’s buffet in the foyer of our home.
I actually only fire a few of them. Most of those that crack or are just plain bad get rendered back into clay. I still have a never-ending supply of failed but fired pieces to experiment with.
Once I’ve gleaned what I can from the glaze experiments they go back to the “yard”. In the case of these four examples, I see they’ve spilled over into the living room. As you can see, when they fail during glaze firing to cone 6, they fail spectacularly.


Stay briny, my friends.
Jeff
01.08.2025 – EOS #01-78,12
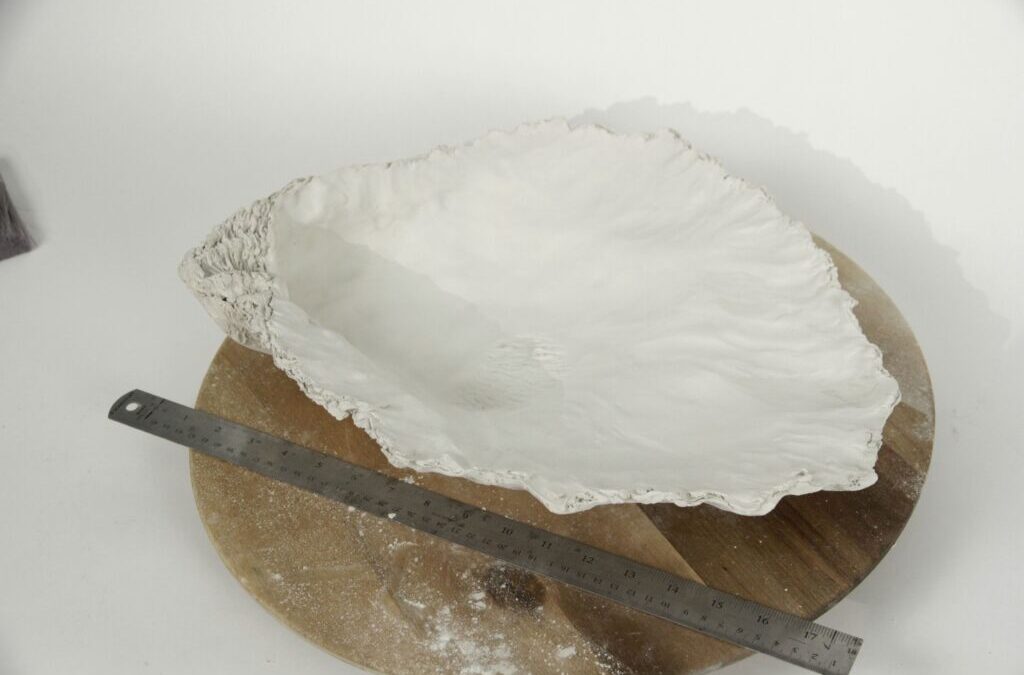
12.30.2024 – #07-84,01 of the Eastern Oyster Study DRY
This is the first study of shell #07-84,01 that came straight from the drying rack this morning. The porcelain clay dries to a cool light grey. Once bisque fired to cone 05 or 1870 degrees Fahrenheit it will have a light warm cream color. Being a mid-fire clay, it will ultimately be heated to cone 6 or 2165 degrees where the unglazed or tinted porcelain will become even warmer in color. At this temperature the clay will become fully vitrified, or transformed into a solid glass like ware. The fact that it has survived the drying process is a great sign! We’ll see how it handles the two firing processes. Check back later and see how it turns out
Cheers!
Jeff.
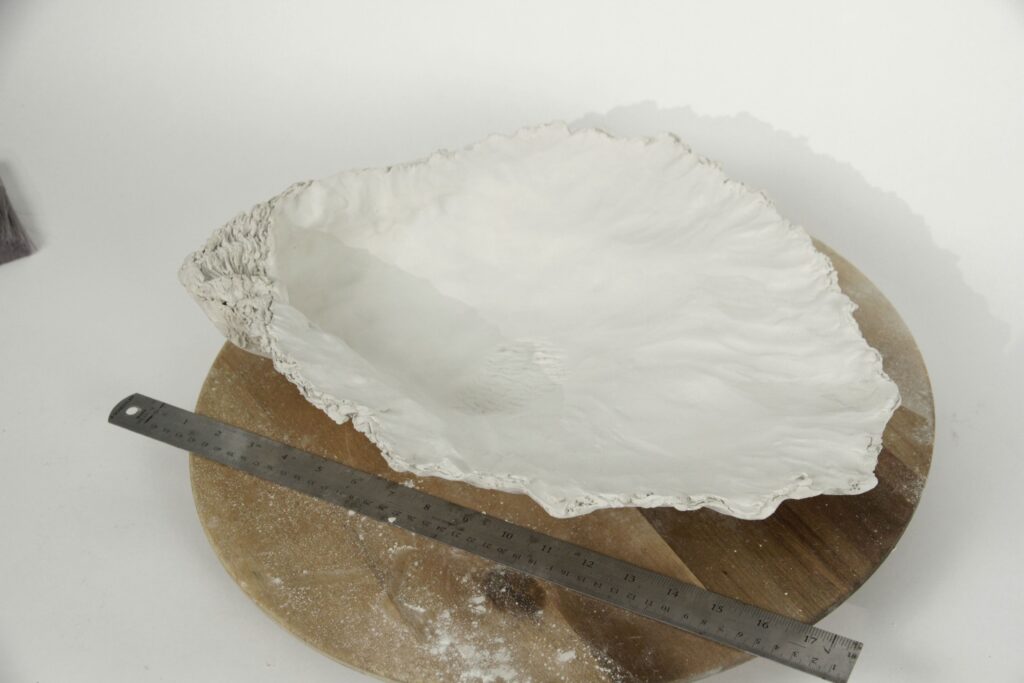

12.29.2024 – The Boneyard
This morning I opened the ol’ Parragon 88 and found two of three pieces of work cracked during bisque fire.
The price I pay for the style of work that turns me on is frequent cracks and failures. Of course a more uniform thickness of the sculpture results in a higher success rate. Yes. I get that. The challenge then is representing a natural oyster and it’s variations of thickness and texture in porcelain in such a way it doesn’t crack during the drying process. If the piece dries completely without cracking, the odds of it surviving the bisque firing intact are pretty good. But with anything, there are no guarantees. Hence, I give you….The Boneyard.



I don’t know why we keep all of my work that missed the mark but we do and have from the beginning. Every couple of months we empty the space and relegate my sad little collection to boxes in the basement or recently to the garden in the yard. Yard Art.
The squirrels seem not to mind and the birds enjoy a good bath. I can live with that.
Jeff